Once again, ClevLine will be present at Interzum Cologne, the international benchmark event for the furniture and bedding industry. As in previous editions, we bring our vision and commitment to show the world a new way of understanding production: more innovative, more conscious, more human.
At this special gathering, we will present our ClevLine, a revolutionary breakthrough that combines advanced automation, extreme precision, and true sustainability. It is not just an evolution in efficiency and productivity: it is a leap towards Industry 5.0. An industry where flexibility, sustainability, and the human-machine factor intertwine to shape smarter, more respectful, and people- and planet-centered production processes.
Thanks to the integration of multiple functionalities and its unique features, we offer the market an innovative concept that breaks with the conventional, completely redefining the quilting industry. Every small detail reflects our commitment to providing not just machines, but genuine solutions that evolve alongside the market’s needs.
At ClevLine, we understand that true progress is not just about producing more, but about producing better: better for companies, better for workers, better for the world. Flexibility, Sustainability, Humanity are not just words accompanying our brand. They are the principles guiding every decision, every innovation, and every advancement towards Industry 5.0.
Would you like to know more about us? Come visit us at Hall 09 | Stand A050-B051.
In a world where efficiency and quality are essential in any production process, automation is presented as a solution that not only improves processes, but also redefines the way in which they are conceived and executed.
At ClevLine, we have always been committed to innovation and technology in order to offer our customers highly flexible solutions that allow them to remain competitive over time. Thanks to these values and after years of study and development, we have provided the market with a totally innovative concept in the mattress industry: A fully automatic production line for quilted panels, covers and borders, which also combines the functionality of a multi-needle and a single/double-needle in the same machine, being able to work with a multitude of framed, centred, tack & jump and continuous designs.
In this publication, we will explore in detail how our automatic production line has come to revolutionise the way you manufacture your mattresses, offering advantages that go far beyond efficiency.
The Conventional Process: A Sequence of Workstations
Let’s first talk about what a conventional production process is like. As you all know, the panel production process starts with the preparation of the rolls of raw material, passing through the different quilting, cutting and hemming stations, ending with the palletisation of the finished panels. Afterwards, these panels are transferred to the assembly section, where they will be used for the top and bottom of the mattress.
But how is this production process usually carried out? It depends on how the production plant is organised and the type of machinery available. Therefore, based on our experience with different customers, you will find below the process faithfully represented by a series of graphics:
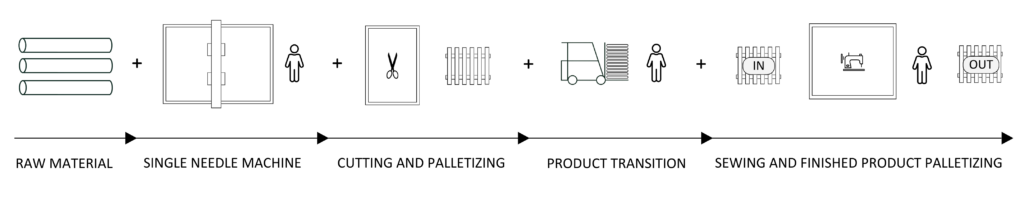
The Automatic Revolution: Integration and Efficiency
Having seen a fairly common conventional production process nowadays, with the number of stations and operators that usually make it up, let us introduce you to how we approach this production process with our CLEVLINE automatic line.
As in the previous case, we start from the raw material rolls to the palletising of the finished product, with the great difference of not requiring any intermediate handling of the product and including all the quilting processes in the same workstation, where only one operator is needed to supervise and control the entire line.
CLEVLINE has a modular architecture, composed of three independent modules that work together for a common purpose:
CLEVONE: Vertical quilting module with four independent sewing heads, qualified to work with all types of designs and a wide variety of materials and thicknesses, guaranteeing a quality finish on each panel.
CLEVPANEL: Automatic hemming module to finish the perimeter of the panel, with high precision in the measurement, reducing the number of workstations and facilitating the subsequent closing of the mattress.
CLEVSTACKER: Automatic stacking module for a higher level of autonomy in the process, eliminating repetitive tasks of low value for the operator.
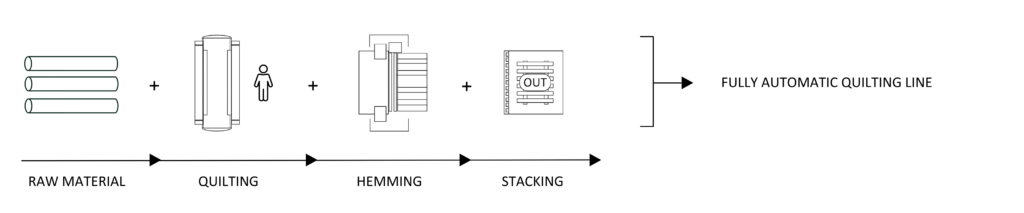
Competitive Advantages:
In addition to improving the production process and the quality of the end product, our automatic line offers a host of unrivalled benefits:
1
Increased Efficiency: With a continuous and uninterrupted work sequence, downtime is minimised, resource utilisation is optimised and, as a result, overall process efficiency is increased.
2
Reduced Costs: By eliminating manual handling of products at different stages of the process, labour and production costs are significantly reduced.
3
Space Optimisation: By integrating all processes into a single workstation, the need for additional space and machinery is reduced, leading to considerable savings in floor space.
4
Improved Product Quality: The automation of processes reduces the risk of damage and flaws during the manufacturing process, ensuring greater consistency in the quality of the final product.
5
Flexibility and Adaptability: Our line allows quick and precise adjustments according to specific production needs, combining the functionality of a multi-needle and single/double-needle in the same machine.
6
Greater Process Control: Automation allows greater control and supervision of the production process, as all parameters and variables can be monitored and adjusted in real time.
7
Operator Care: It frees the operator from repetitive and routine tasks, allowing them to focus on higher value activities such as production process supervision, quality control and problem solving, providing them with greater job satisfaction.
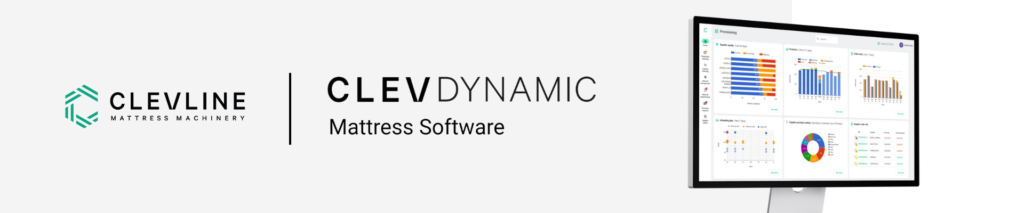
What does it take to digitize your mattress manufacturing plant?
The era of Industry 4.0 is headed by a concept that many people are unfamiliar with or confused about; digitization.
Broadly speaking, it is based on the use of digital technologies to change a business model and provide new opportunities and ways to produce revenue and value.
Today, it has become a requirement to maintain and boost competitiveness in an increasingly automated industry; an essential to not fall behind in the market and to acquire a wide range of advantages for your mattress production plant and the rest of the company.
Another aspect that often creates discrepancy among many users is the false belief that it is a change that needs to be implemented in a radical way, but nothing could be further from the truth. At ClevLine we always support the theory that it can and should be implemented progressively, as it completely transforms the way in which companies operate and make decisions.
Why make this change?
Making the decision to digitize your mattress factory is also often seen as a difficult challenge to tackle, as it seems to involve multiple implications and significant changes.
As a company, we are often looking for comfort and wellbeing, which prevents us from seeing the advantages of leaving our comfort zone. And the fact is that digitalisation represents a big change, yes, quite a big change, but it is about implementing a new way of doing things, to take the leap to a higher level, as far as management is concerned.
On the other hand, the concept of digitalisation and automation has always been accompanied by the fear of replacing and substituting the human team, but the challenge lies in convincing the production team that, far from being replaced by technology, it will free them from monotonous tasks and allow them to work more efficiently and feel more productive, thanks to being able to take charge of functions that add value to the company.
As mentioned before, the digitisation of a mattress manufacturing plant is not an easy process, as it involves multiple factors, so it is crucial to map it out properly in order to achieve lasting success. Ideally, changes should be implemented gradually, avoiding changing the way of working completely from the very beginning.
How is it done and what does it entail?
We would like to start this brief explanation with a concept that you may be familiar with: The Internet of Things (IoT). Basically it is about connecting physical elements to the Internet, in this case, to our ClevDynamic system.
Our way of doing this is through the monitoring of the factory’s equipment in order to collect data in real time, which, in turn, almost instantaneously, is reflected and presented in a graphical and representative way for the person in charge, with the aim of providing and facilitating decision making. We do not want to create a huge flow of numerical data that the user must take to other external applications or be forced to generate their own Excel pivot tables to obtain information from a huge amount of data.
The control and analysis of the data collected during manufacturing is reflected through an easy-to-interpret interface that allows faults, anomalies and incidents in the process to be detected, so that rapid action can be taken and predictions can be made about future situations.
ClevDynamic creates a digital model of the manufacturing process of each product, bringing together all the information about its characteristics, materials and procedures from its technical data sheet in a single place.
At the end of the day, it is a tool that allows the optimisation of industrial production processes, enabling the reduction of delivery and supply times, and significant cost savings and inventory optimisation.
If you would like to learn more about digitalisation and how it can benefit your company, contact us now! We will be happy to help you make the leap to Industry 4.0.
We are very pleased to announce you that we are going to be exposing our automated panel manufacturing line at the international fair INTERZUM Cologne, which takes place from May 09 to 12 of this year.
Our team will be there to provide you with all the information you need and answer any questions you may have about the latest updates we have developed and incorporated since the last edition.
Don’t miss out on this opportunity to explore the latest trends and technologies in the industry. Come and visit us in Hall 9.1, Stand A050-B051, we will be delighted to see you!
The first 100% digital edition of Interzum will take place from May 4 to 7, 2021, and ClevLine will be present at it!
Due to the current situation, a completely virtual stage has been created to hold one of the leading trade fairs in the mattress sector.
From Interzum @ home you will be able to speak directly with our team, arrange a visit to see the complete line in full operation, download our catalogs, and see everything we have prepared for you.
Soon we will provide the link so you can come and be part of this new experience!
Never has been so easy to be at Interzum
In the times we are living, we believe the best way to be near you is open the doors of our company.
ClevLine wishes you all the best, let’s get through this together!
The new quilting machine that, under the ClevLine brand, is designed to respond to the new trends and demands of the Mattress Industry.
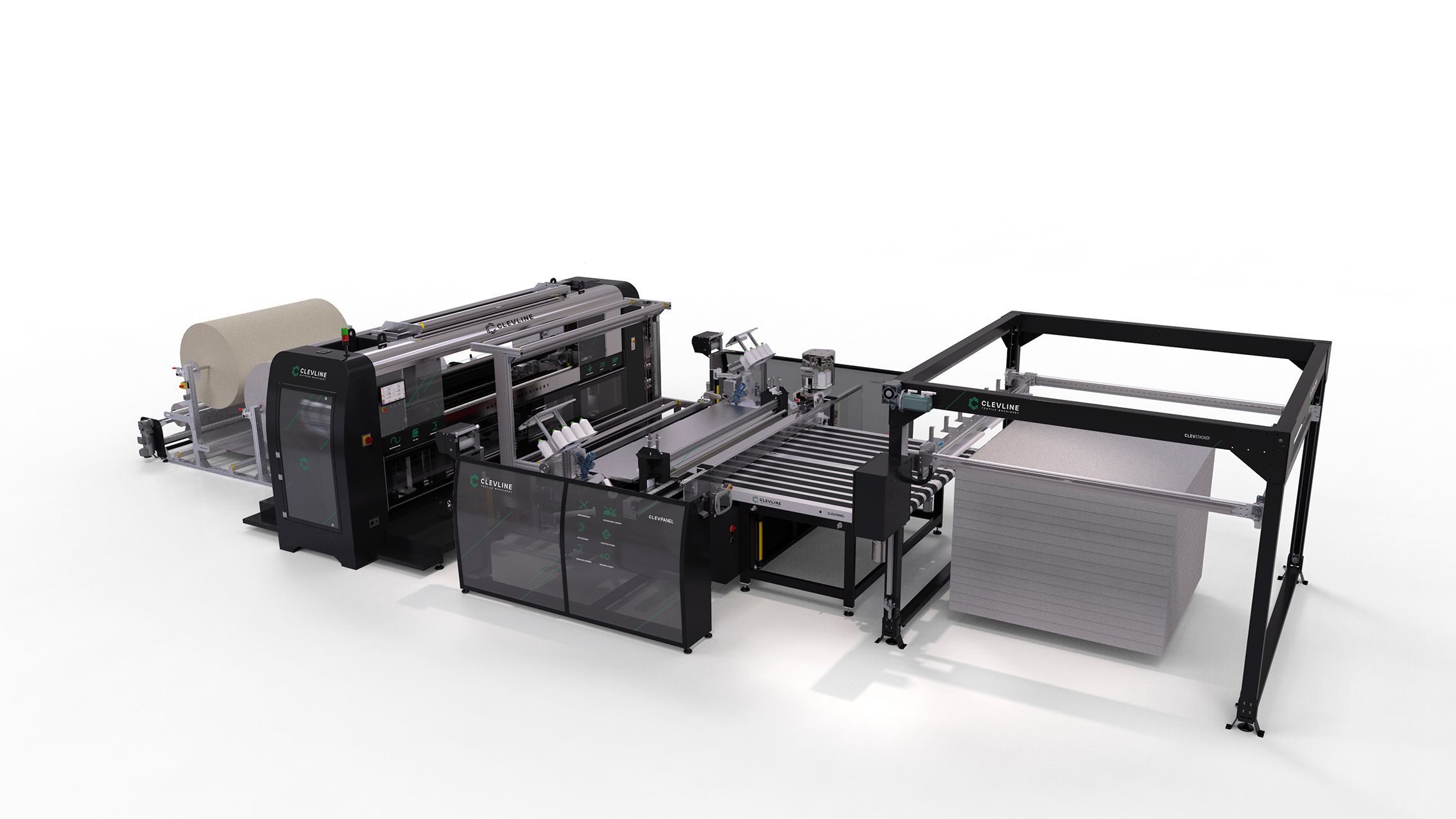
The duplication of production, the optimization of manufacturing times, the conscious use of material and its limited occupation in plant are some of the aspects that we have taken into account when developing ClevOne.
Its own technology and a structure composed of functional blocks specifically created and developed for ClevOne, make it the best option to produce quilted material.
Designed to adapt to new trends
The new trends in terms of composition, materials and fabrics make the Mattress Industry, a sector in constant change, which has motivated us to create a quilter capable of making a difference. For its design, we take in count the needs and expectations observed in our customers, and therefore ClevOne works in vertical position, occupying 35% less in plant than conventional quilting machines.
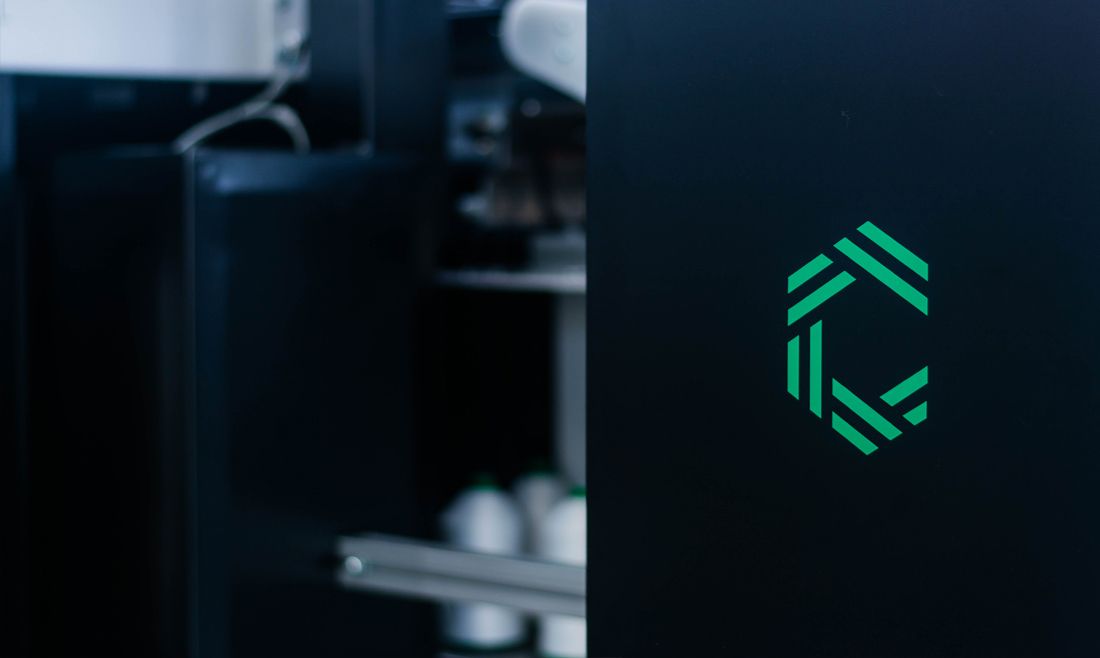
Our DNA values captured into this new identity.
Proven experience in sewing technology
This is possible thanks to our sewing technology available to their heads, in which we have turned all the experience and knowledge acquired during the last decade.
With more than 300 sewing heads manufactured for ClevPanel, our refined know-how and an engineering team recognized as Motion Control Specialist by Siemens, the ClevOne sewing heads are capable of processing materials between 1 and 8 cm thick without any difficulty.
This is due to our development of Quilting Motion System, through which the flow of material is done vertically synchronizing with the transverse movement of the sewing heads, obtaining a quality seam in all areas of the design of the quilted material.
ClevDynamics
But undoubtedly, one of the strongest points of ClevOne is the technology that it integrates.
It has ClevDynamics, a module developed entirely by our specialized programming team, in which the day-to-day needs of the production plants have been contemplated, allowing the connection of different departments with ClevOne, from two different profiles: Operator, focused to the operators and Connect, focused on the production responsible.
Through these two routes, the production queue will become dynamic, feeding as the production manager adds the production orders whose references will automatically regroup facilitating the work of the operators in plant.
Del 21 al 24 de Mayo de este año se celebra en Colonia una nueva edición de la prestigiosa Feria Internacional INTERZUM.
A new edition of the prestigious INTERZUM International Fair is held in Cologne from May 21 to 24 of this year.
This event is highly valued by the rest equipment manufacturers sector, having several pavilions dedicated exclusively to industrial machinery for that sector. You can visit us in Hall 9.1 Stand B030 C031
If you want more information about this event, you can click on this link and visit the website of the Fair www.interzum.com